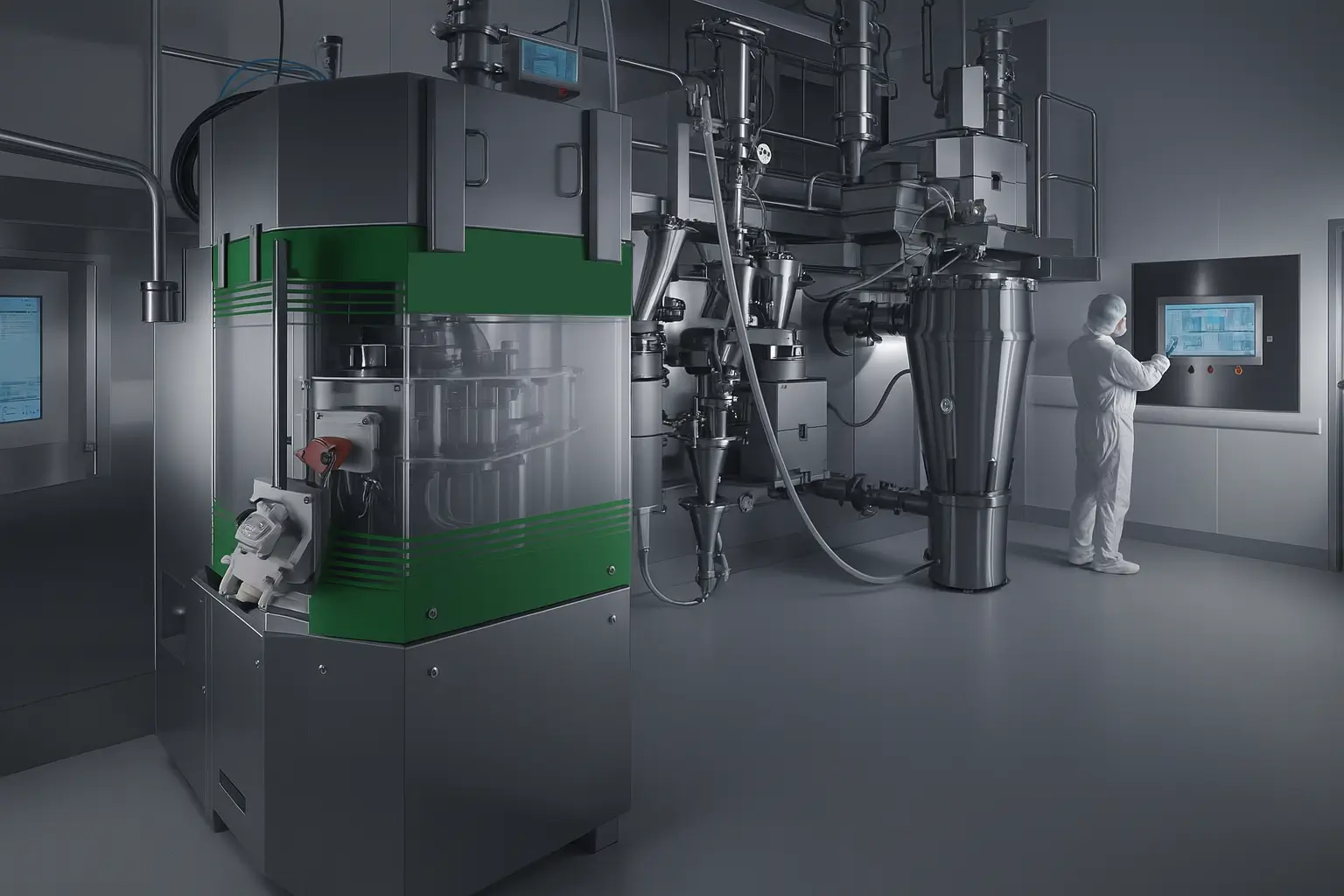
In the pharmaceutical industry, precision is paramount. When it comes to powder processing, achieving the right particle size directly affects bioavailability, solubility, and stability. But choosing the most effective method, micronisation or milling, requires careful consideration of multiple factors.
At Schematic Engineering Industries, we help pharmaceutical manufacturers assess the advantages and limitations of both methods to match their process goals, product sensitivity, and regulatory needs. Below, we break down the core differences and practical implications of each approach.
Micronisation is a high-precision powder processing method that reduces particle size using fluid energy, typically through a jet mill. Particles collide with each other at high velocity, leading to size reduction without mechanical contact.
Key Features:
Schematic Engineering Industries offers jet mills with closed-loop configurations that integrate easily into cleanroom setups and support sterile production.
Milling encompasses a range of mechanical size-reduction techniques, such as hammer mills, pin mills, and ball mills. These systems use physical impact, shear, or attrition to fracture larger particles.
Key Features:
While milling is effective for many applications, its particle size range is generally broader and less precise compared to micronisation. At Schematic Engineering Industries, we supply both high-shear and low-shear milling solutions, adapted to your product's characteristics.
Particle size plays a central role in pharmaceutical formulation. Smaller particles increase surface area, improving dissolution rates and bioavailability, especially in oral dosage forms. However, going too small can affect powder flow, compression, and stability.
Here’s a typical classification in pharmaceutical terms:
Particle SizeApplication Use>500 micronsGranulation, direct compression100–500 micronsGeneral tablet production10–100 micronsControlled-release formulations<10 micronsInhalable drugs, rapid-dissolution tablets
Micronisers are best when consistency and particle size below 10 microns are essential. Milling is more appropriate for initial size reduction or when working with less sensitive materials.
At Schematic Engineering Industries, we guide clients in selecting systems based on material properties, final dosage requirements, and regulatory expectations.
When comparing micronisers and milling systems, the differences go beyond particle size. Factors such as energy usage, cost of ownership, and containment complexity also impact your selection.
Schematic Engineering Industries specialises in providing integrated containment systems for both micronisers and mills, including CIP/SIP options, gloveboxes, and barrier isolators.
Opt for micronisers when:
Many of our clients at Schematic Engineering Industries in the biotech and oncology sectors choose micronisation for its ability to preserve product integrity and meet strict purity requirements.
Choose milling if:
We support milling integration into upstream or pre-processing stages, often combined with sifting, blending, or granulation equipment to create a cohesive process line.
At Schematic Engineering Industries, we don’t offer generic equipment, we deliver process-specific powder handling solutions engineered for performance, safety, and compliance. Whether you're choosing between micronisers or mills, we help you:
From concept to commissioning, our engineering team ensures your chosen method aligns with your facility, regulatory scope, and production objectives.
Unsure which powder processing system fits your pharmaceutical process? Contact the team at Schematic Engineering Industries to explore tailored micronisation or milling solutions designed to optimise your operations.