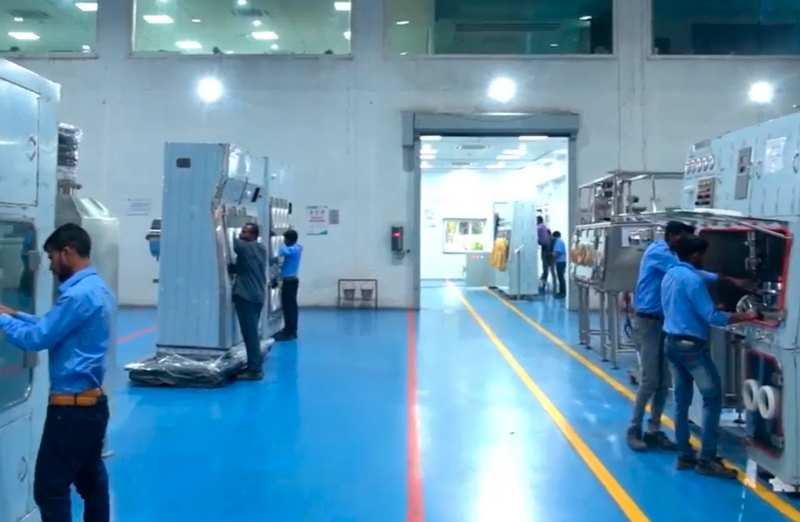
Powder handling is a fundamental aspect of pharmaceutical manufacturing, but it presents several challenges that can affect efficiency, safety, and product integrity. Handling fine powders for drug production requires precise control to prevent contamination, loss of material, and inconsistencies in formulation. Several key factors contribute to difficulties in powder transfer.
Fine pharmaceutical powders tend to become airborne during transfer, leading to contamination risks and health hazards for operators. Excessive dust can also compromise the cleanliness of manufacturing areas, making it difficult to maintain regulatory compliance.
During transfer processes, powder spillage or adherence to equipment surfaces results in material loss. Over time, this can significantly impact production efficiency and increase manufacturing costs.
In multi-product pharmaceutical facilities, powder residue from one batch can mix with another, leading to cross-contamination. This is particularly concerning in facilities handling potent drugs or allergenic compounds.
Certain powders have poor flow characteristics, making them difficult to transfer smoothly between process steps. This can result in inconsistent dosing, clogging of transfer lines, and inefficiencies in mixing and blending processes.
Inadequate containment during powder transfer exposes operators to hazardous materials. Prolonged exposure to active pharmaceutical ingredients (APIs) can pose health risks, necessitating the use of containment solutions to protect workers.
To address these challenges, pharmaceutical manufacturers utilise specialised equipment designed to improve powder transfer efficiency while minimising contamination risks and material loss.
Split butterfly valves (SBVs) are widely used in pharmaceutical powder transfer to ensure contained and contamination-free movement of materials between processing units.
How SBVs Improve Powder Handling:
Micronisation is a critical step in pharmaceutical manufacturing, used to achieve the required particle size for better solubility and bioavailability of drugs. Micronisers, such as jet mills, provide controlled particle size reduction.
Benefits of Micronisers:
Vacuum conveying systems are an effective method for transferring pharmaceutical powders without creating airborne contamination. These systems use negative pressure to move powders through enclosed pipelines.
Why Vacuum Conveyors Are Beneficial:
For handling highly potent or hazardous pharmaceutical powders, containment isolators provide a fully enclosed environment, ensuring maximum protection for operators and products.
Advantages of Containment Isolators:
Implementing advanced powder handling equipment such as split butterfly valves and micronisers significantly improves pharmaceutical production efficiency and safety.
Traditional powder handling methods often lead to material loss, impacting overall production efficiency. Split butterfly valves create a secure transfer system, reducing the amount of powder lost during processing. Similarly, micronisers provide precision milling, ensuring that raw materials are efficiently utilised without excess waste.
Maintaining precise particle size is critical in pharmaceutical formulations. Micronisers enable uniform particle size distribution, improving drug absorption and effectiveness. Additionally, split butterfly valves ensure that powders remain uncontaminated during transfer, preserving product integrity.
Controlling powder movement is essential for preventing cross-contamination in pharmaceutical facilities. Split butterfly valves allow contained transfer between production stages, while micronisers ensure precise control over particle size without unwanted blending of different substances.
Handling potent pharmaceutical powders requires strict safety measures to protect workers from inhalation exposure. Containment solutions such as SBVs and micronisers reduce the need for manual handling, lowering the risk of exposure to hazardous compounds.
Pharmaceutical manufacturers must adhere to Good Manufacturing Practice (GMP) regulations, which mandate strict containment and powder handling procedures. The use of split butterfly valves, micronisers, and vacuum conveyors ensures compliance with regulatory standards, reducing the likelihood of product recalls or quality issues.
Effective powder handling is essential for optimising pharmaceutical production processes. Overcoming challenges such as airborne contamination, product loss, and cross-contamination requires the adoption of specialised equipment designed for precision and safety. Split butterfly valves, micronisers, vacuum conveyors, and containment isolators all contribute to improved efficiency, better product quality, and enhanced operator protection.
Manufacturers investing in advanced powder handling solutions not only improve safety and compliance but also enhance overall operational efficiency, ensuring consistent and high-quality pharmaceutical products.