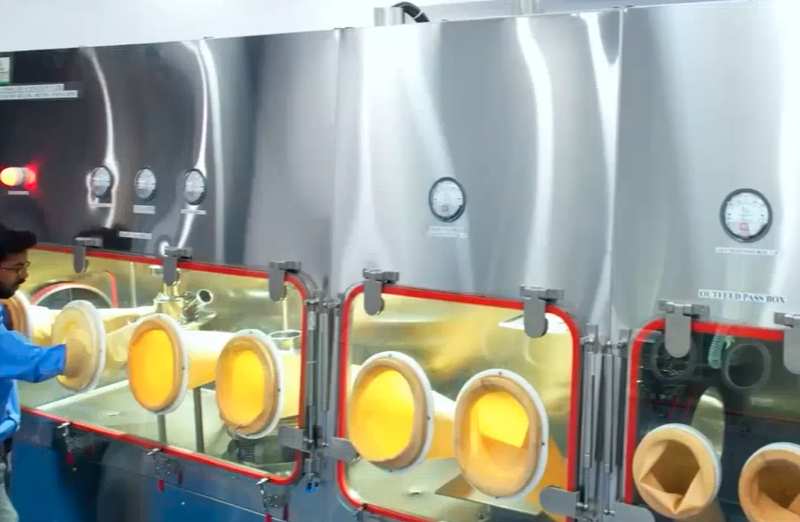
Pharmaceutical manufacturing requires a controlled environment to ensure the safety of both the product and the personnel involved in its production. Containment plays a critical role in preventing airborne contamination, safeguarding operators from hazardous substances, and maintaining compliance with stringent industry regulations. Whether through the use of isolators, glove boxes, or other containment systems, manufacturers must adopt effective strategies to uphold safety and product integrity.
In this article, we explore the risks of airborne contamination, the role of containment systems, and the key industry regulations that guide pharmaceutical manufacturing.
Pharmaceutical products must be free from contaminants to ensure efficacy and safety. Even the slightest contamination from airborne particles, microorganisms, or chemical residues can compromise the integrity of the final product. This can lead to:
Many pharmaceutical ingredients, particularly active pharmaceutical ingredients (APIs) and highly potent compounds, pose health risks to operators. Without proper containment, exposure to these substances can result in:
Contaminants released during the manufacturing process can also pose risks to the surrounding environment. Without effective containment measures, pharmaceutical waste and airborne particulates may:
Isolators are fully enclosed containment systems designed to provide a high level of protection by creating a controlled, sterile environment. They are widely used in pharmaceutical manufacturing for tasks requiring a contamination-free workspace.
Glove boxes are another essential containment solution, allowing operators to handle materials in a controlled environment without direct exposure. These enclosures feature built-in gloves that allow precise manipulation of pharmaceutical products.
Selecting the appropriate containment solution depends on various factors, including:
Pharmaceutical manufacturers must comply with strict regulations to ensure product safety, worker protection, and environmental responsibility. Some key regulations governing containment in pharmaceutical manufacturing include:
GMP guidelines, established by regulatory bodies such as the FDA (Food and Drug Administration) and the EMA (European Medicines Agency), outline requirements for cleanroom design, contamination control, and proper use of containment systems.
GMP compliance includes:
To minimise the environmental impact of pharmaceutical production, manufacturers must adhere to regulations set by the Environmental Protection Agency (EPA) and equivalent organisations worldwide.
These standards address:
As pharmaceutical products become more complex and potent, containment technologies must evolve to meet increasing safety demands. Some emerging trends in pharmaceutical containment include:
New innovations in isolator and glove box technology are enhancing contamination control and operator safety. Features such as automated decontamination, pressure control systems, and integrated monitoring are improving the reliability of containment solutions.
The adoption of single-use isolators and disposable containment systems is gaining traction. These solutions reduce the risk of cross-contamination, eliminate the need for extensive cleaning, and enhance flexibility in pharmaceutical production.
Robotic systems are being integrated into containment solutions to minimise human interaction with hazardous materials. Automation helps improve precision, efficiency, and safety in pharmaceutical processing.
Containment is a vital aspect of pharmaceutical manufacturing, ensuring product integrity, operator safety, and environmental compliance. The risks of airborne contamination highlight the need for effective containment systems, such as isolators and glove boxes, to safeguard both personnel and pharmaceutical products.
Regulatory compliance plays a crucial role in maintaining high standards within the industry, with guidelines such as GMP, occupational safety regulations, and environmental protection laws shaping containment practices. As technology advances, automation, single-use solutions, and enhanced containment systems will drive the future of pharmaceutical manufacturing.
By implementing robust containment strategies, pharmaceutical manufacturers can uphold safety, efficiency, and regulatory compliance, ensuring that their products remain safe and effective for consumers.
Looking to enhance your pharmaceutical containment strategy? Schematic Engineering Industries offers precision-engineered isolators, glove boxes, and material handling systems designed for HPAPIs, sterile processing, and sensitive pharmaceutical environments.
Our team will work closely with you to assess your facility's specific needs and deliver containment solutions that prioritise operator protection, product integrity, and full compliance with GMP and environmental standards.
Contact us today to discuss your project and find out how our containment systems can support your manufacturing operations.