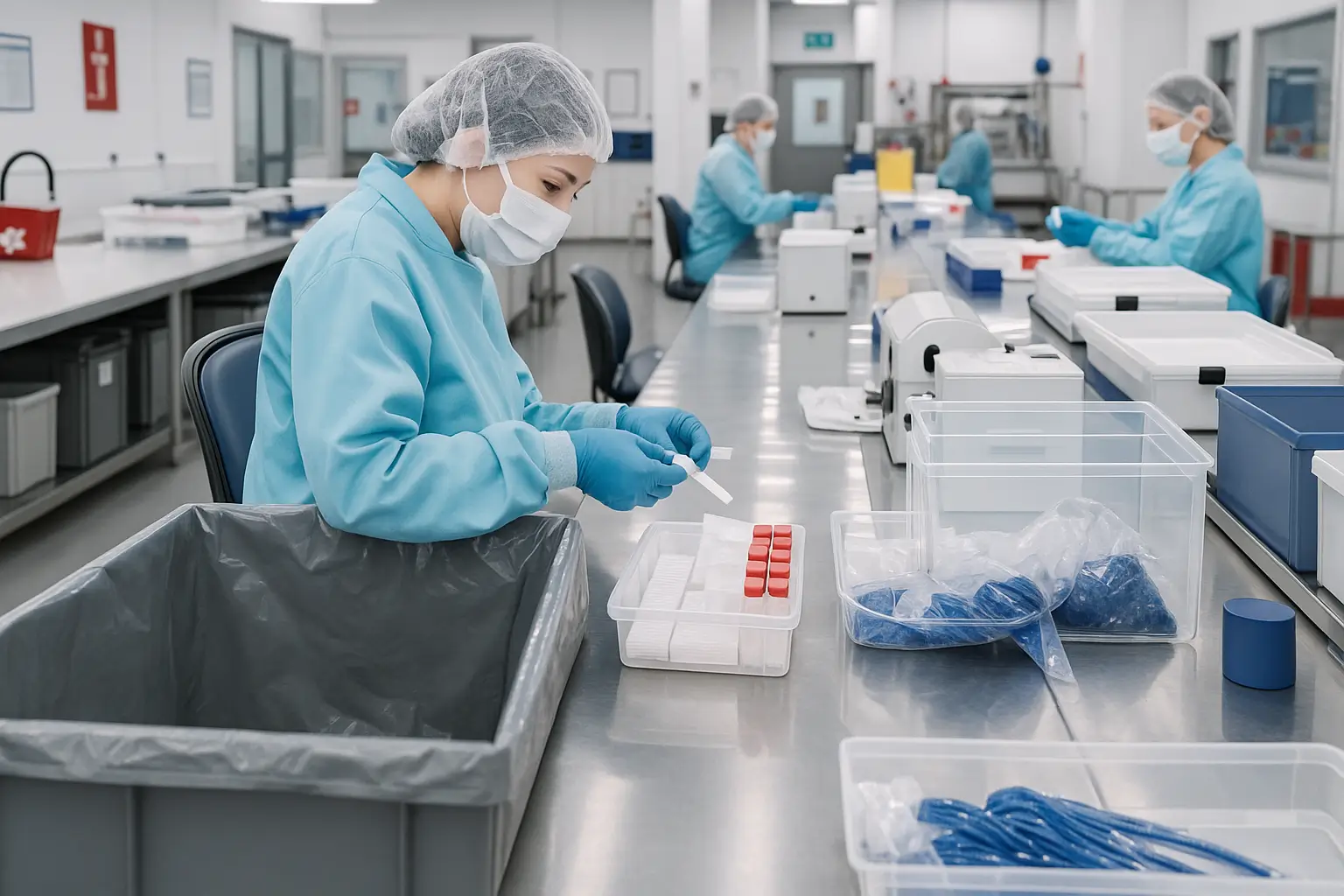
Cleanroom environments are designed for absolute control. In sectors such as pharmaceuticals and biotechnology, maintaining sterility isn’t just a preference—it’s a regulatory mandate. Every piece of equipment and every movement of material must conform to the strictest standards to prevent contamination. At Schematic Engineering Industries, our role is to ensure that the material handling systems you rely on contribute to, rather than compromise, your cleanroom’s integrity.
A cleanroom functions as a barrier against unwanted particles, microbes, and other contaminants. Yet, even the most well-designed space can become compromised if material handling is not properly managed. Whether you're transferring powders, managing intermediates, or moving finished goods, the path that material takes is just as critical as the final product itself.
One of the core challenges in cleanrooms is the balance between operational efficiency and contamination control. Every piece of equipment must perform its function without introducing external threats. This is why our material handling systems at Schematic Engineering Industries are built for hygienic, sterile, and controlled operation.
Our portfolio includes:
These systems are designed to reduce manual intervention, streamline product flow, and most importantly, maintain air cleanliness and product purity.
Despite stringent regulations and high-end facilities, pharmaceutical manufacturers often face persistent cleanroom issues linked to material handling. Among the most common:
At Schematic Engineering Industries, we address these issues head-on with closed-loop systems, automated transfers, and modular containment zones. Our engineering team works closely with cleanroom designers to ensure seamless integration between equipment and architectural constraints.
Regulatory bodies such as the MHRA, FDA, and EMA impose rigorous cleanroom classifications and validation protocols. One critical focus: containment during material handling. Improper containment doesn’t just lead to failed audits—it can shut down an entire production line.
That’s why we at Schematic Engineering Industries take containment seriously. Our isolators and transfer systems are engineered with:
These systems maintain both operator safety and product sterility, meeting or exceeding regulatory expectations. More importantly, they ensure consistent, repeatable performance—a cornerstone of any compliant manufacturing operation.
Maintaining cleanroom integrity is not just about equipment—it’s about how that equipment is used. To optimise your cleanroom’s efficiency and compliance, Schematic Engineering Industries recommends the following practices:
Our clients often see a measurable drop in contamination events after implementing Schematic’s automated and contained handling solutions. The reduction in deviation reports and batch rejections translates directly into cost savings and higher throughput.
Every cleanroom is unique, and a one-size-fits-all approach doesn’t work. At Schematic Engineering Industries, we customise every solution to fit your facility’s layout, process requirements, and regulatory context. Whether you’re managing potent APIs, working with sterile injectables, or handling sensitive biotech cultures, our team designs systems that adapt to your needs.
We consider:
The result is a solution that protects your process, your personnel, and your product without compromising throughput or increasing complexity.
With decades of experience serving regulated industries, Schematic Engineering Industries has become a trusted name in high-performance material handling. Our commitment goes beyond equipment, we become partners in your compliance and production journey.
Whether you're retrofitting a legacy cleanroom or building a new sterile facility, our team is ready to assist. We provide:
When cleanroom integrity is non-negotiable, Schematic Engineering Industries delivers the tools and expertise to keep you compliant and competitive.
Ready to enhance your cleanroom with precision-engineered material handling systems? Contact the team at Schematic Engineering Industries today to explore tailored solutions that fit your facility and production goals.