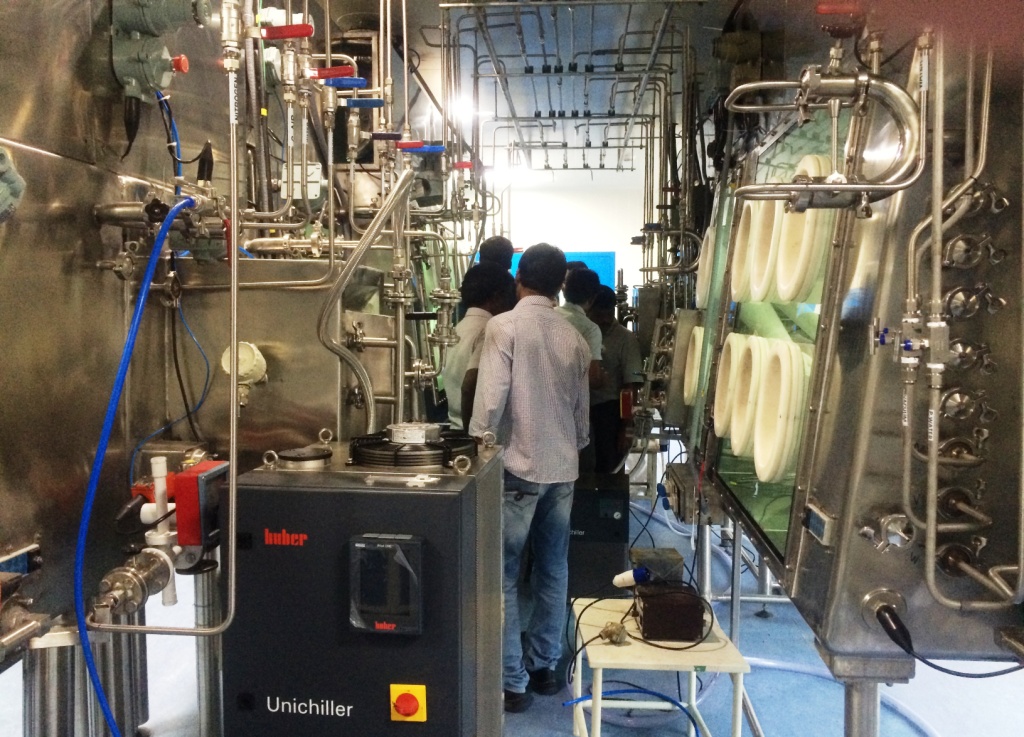
Barrier isolators are an essential element of all modern chemical and pharmaceutical process plants as they keep operators safe and the product free from contamination.
Isolator applications range from Reactor charging to Sieving, Dryer discharge to Granulation and their construction typically involves a complex pressurised system including multiple filters, regulators, instruments, chillers and valves together with miles of pipework, associated fittings and electronic circuitry.
It is therefore not surprising that these complex systems periodically go wrong whereby filters get blocked, airlines and connections start to leak, pneumatic cylinder seals fail, electronic interlocks seize, and gloves become worn and unusable. At the precise micron levels of control that barrier isolator systems operate, these circuit and system failures are not always initially obvious or apparent to users.
As with running a car, the deterioration in the car’s fuel-economy or acceleration/braking may not be immediately apparent to the user but this will, over time, start to impact on performance especially in times of breakdown. Likewise, but on a much higher scale of importance, a deterioration in the barrier isolator system performance will not only put laches and crores of processed goods in danger, but also impact on operators health endangering their respiratory system, skin and senses.
Occupational Exposure Limits (OEL’s) are amongst several key performance safety mechanisms which barrier isolators must comply with. Maintaining such high control standards is a task in itself, however best practice techniques, regulations and legislative equipment compliance standards change over time as does the accompanying documentation headaches, therefore many plant managers are now seeking technical authority support in this area.
Schematic Engineering Industries is based in the UK and Hyderabad, India and are experts in designing, manufacturing, installing and commissioning complex and bespoke barrier isolator systems, primarily for the pharmaceutical and chemical industry sectors. Furthermore, Schematic specialize in providing value-adding services to clients and in full cooperation with the client’s team and production schedules, they operate Annual Maintenance Contracts (AMC’s) for the validation of the clients installed Barrier Isolators no matter who originally supplied them.
Under these equipment healthcare contracts, Schematic perform the complete overhauling of the clients existing isolators with the objective to bring them back to an "as new" condition in a phased manner throughout the year. Each barrier isolator overhaul includes changing all necessary spares, reassembly and testing the equipment in accordance with international, national and/or company specific standards to a pre-decided time table. The AMC also includes for emergency site visits to address any problems encountered during regular barrier isolator operation
During the barrier isolator re-qualification phase, Schematic typically carryout isolator validation and healthcare testing including;
Like the periodic servicing of your car, this barrier isolator value adding service offers plant managers a ‘complete peace of mind’ over the quality and performance of their equipment, allowing them to concentrate their internal resource to maximise production output while Schematic take care of the equipment problems, validation and documentation issues.
If you are interested about hearing how Schematic can remove the "barrier isolator validation headaches" from your plant, please contact us at Tel: +91 40 2309 4082 or email: info@schematicind.com or visit our website: www.schematicind.com